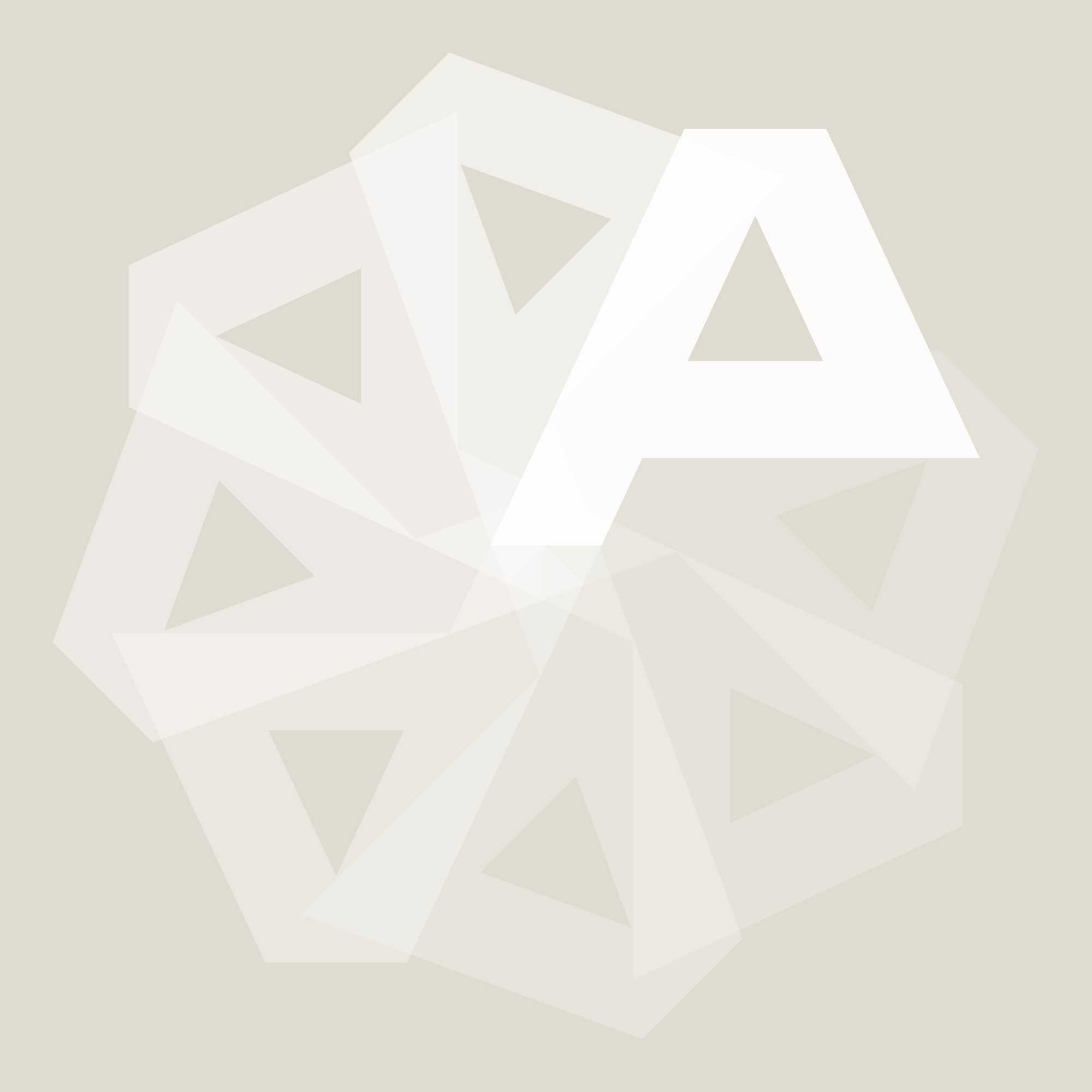
Navigating Supply Chain Disruption
December 10, 2021
It should not be a surprise at this point that supply chains globally have been significantly disrupted. Newspapers report daily on the number of container ships waiting to offload in various ports around the world. Social media feeds feature families unable to get kitchen appliances installed or toys delivered in time for holidays. TV presenters highlight challenges faced by a range of local businesses struggling to create and supply goods.
The causes of such disruption are many, but three are especially critical: the impact of COVID-19 on supply and demand, COVID-19 restrictions that have limited business operations and the compounding challenges caused by kinks in supply chains.
COVID-19 drove unprecedented sudden and dramatic shifts in both demand and supply. Supply chain managers have always had to be nimble to respond to challenges in increasingly complex chains. But past disruptions tended to be local or regional, typically caused by environmental disasters or other emergencies. The pandemic, however, hit countries globally and nearly simultaneously.
Locked-down customers quickly changed up their shopping habits to feature fewer “experiences” like eating out or travel and instead splurged much more on home remodeling, home entertainment options, and food delivery. Firms struggled to manage such rapid adjustments in demand.
In some cases, the overall demand may have been consistent, but firms were still caught out. For example, customers may have used the same overall amount of toilet paper, but as more customers were using the product in homes and not in institutional settings like offices or schools, companies struggled to deliver packaging appropriate for homes and work out distribution methods better suited to non-institutional customers.
Supply also shifted sharply. Firms that had previously sent toilet paper in basic paper packaging inside large plain brown boxes had to quickly find sufficient plastic wrapping, get it printed with appropriate branding, and procure enough smaller boxes to deliver to retail stores.
Many companies discovered that supply was constrained by over-reliance on one supplier of a critical part of the supply chain. Often, it was not the obvious elements of a product that were at risk, but the often-unnoticed raw materials, parts or components like cardboard boxes or rubber gaskets that became impossible to find and order.
To compound the challenges of navigating demand and supply shocks, companies were often forced to struggle without sufficient staff. Employees were out due to the pandemic or were prevented by various government lockdowns from leaving their homes.
Firms scrambled to get staff classified as “essential services.” Even this may not have solved all the challenges. If the toilet paper firm was essential, it may have been the case that cardboard box manufacturers were not similarly situated, leaving the toilet paper company unable to deliver their products.
The inability of the cardboard manufacturer to deliver boxes then created compound issues for supply chains of all sorts. The box company quickly became overwhelmed with back orders, shifting demands from traditional customers, and an inability to meet the needs of new customers.
The box manufacturer may have been further constrained by insufficient supplies of paper pulp, delivered on time, and as needed. The urgent demands of the box producer to get raw materials may have led the company to agree to higher shipping prices to get stock into place faster.
Similar behavior by companies across the supply chains and around the globe compounded the rapid rise in shipping costs. Firms in shipping and other logistics operations were also constrained by their inability to get their own staff in and out of various markets to continue to provide services. In the early part of the pandemic, especially, governments were deeply reluctant to allow mariners or cargo pilots to disembark and it was a major struggle to work out how to allow movement of critical personnel.
Each time chains adjusted to manage disruption, COVID-19 threw up new challenges. The rise in new variants led governments to continuously shift advice on lockdowns. Navigating these constant adjustments has often meant that previous kinks in a supply chain cannot be fully resolved before a new set of issues surface.
While COVID-19 has had a global impact, the specific consequences of the pandemic have varied across markets. Some have been relatively unaffected, with domestic “life” continuing unimpeded by COVID-19 concerns. Other locations have been dramatically affected with significant illness and loss of life. Governments have kept some economies open and have pushed hard lockdowns for lengthy time periods in others.
As a result, firms in some locations have been more significantly impacted than companies elsewhere. The export-oriented governments in Asia have tended to provide greater flexibility for operating, particularly for export goods, than might be found elsewhere. For example, the classification of essential goods operators can be quite broad, allowing firms to continue operating with fewer restrictions that might otherwise have been expected given strict COVID-19 protocols in specific markets.
As the pandemic enters the third year, supply and demand challenges should start to moderate. But firms and governments will continue to navigate changing health conditions, with the strong possibility of future shutdowns in operations in some markets. Such extended disruptions in supply chains will make addressing kinked chains harder to resolve.